5月18日,中山三角镇,和超高装(中山)科技有限公司的超导腔生产车间内,原哈尔滨工业大学材料学院焊接系教授,和超高装(中山)科技有限公司创始人、董事长何景山正俯身计算机前,调试新到的进口真空电子束焊机。这台全球最大型的设备正式运行后,将实现中山产超导腔产品的全工艺覆盖。而就在三个月前,这家工厂的超导腔年产量突破150套,让中国在这一高端装备领域彻底超越国际竞争对手,迈入技术与产量“无人区”。
带团队南下中山
“超导腔是粒子加速器的‘心脏’,用于提升粒子束的能量与亮度。但它的民用场景同样广阔——医疗领域可用于精准疾病诊断,通信领域能提升信号稳定性,能源领域可优化清洁能源利用,航天领域则能减轻设备重量……”当天,在何景山的公司里,他给记者介绍道。
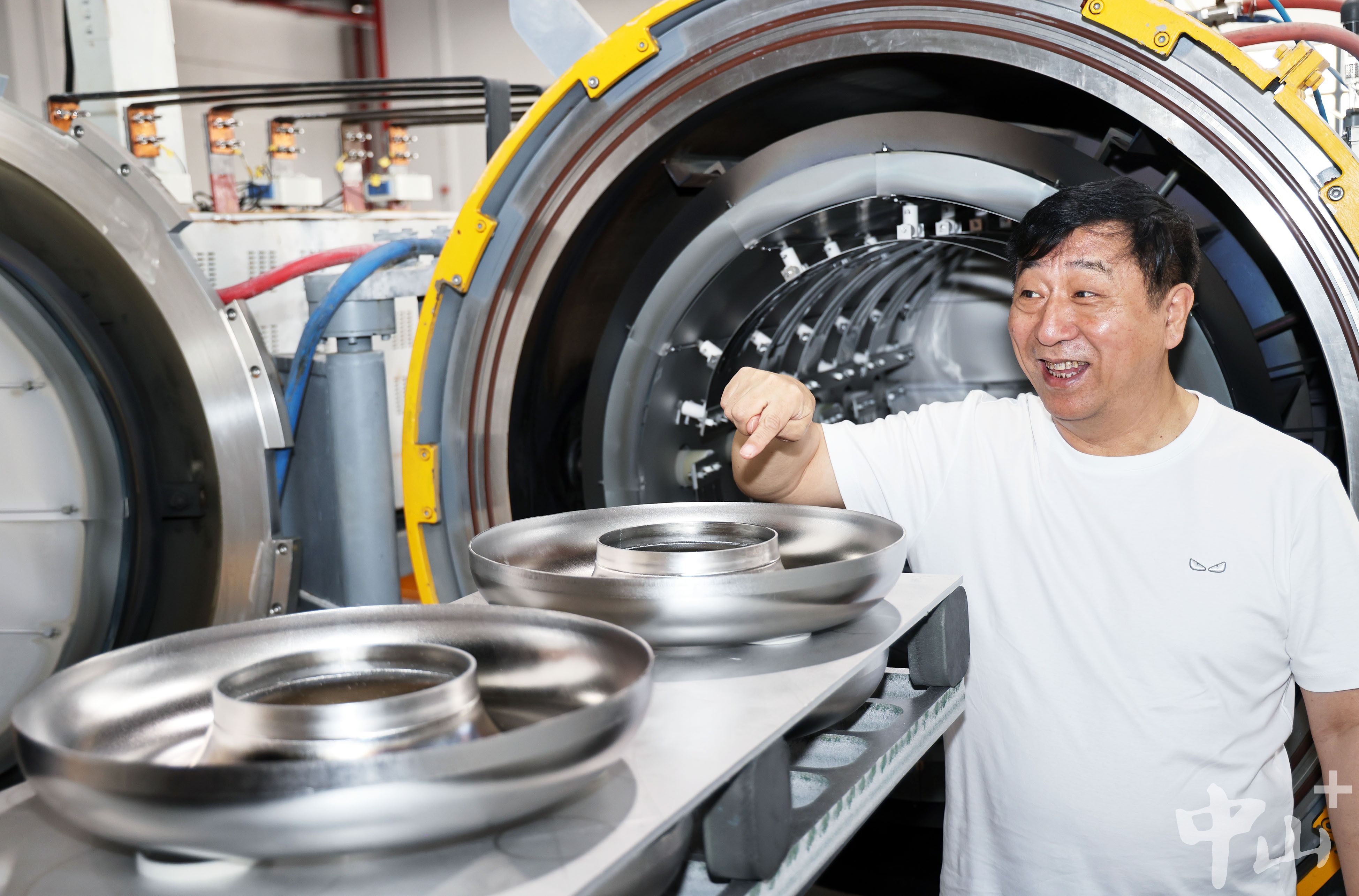
何景山创业的故事颇吸引人:2017年,在哈尔滨,何景山作为哈工大焊接国家重点实验室核心成员,在完成“神七”航天服水升华器焊接工艺攻关之后,他就作出一个惊人决定:退休创业,率队南下中山。
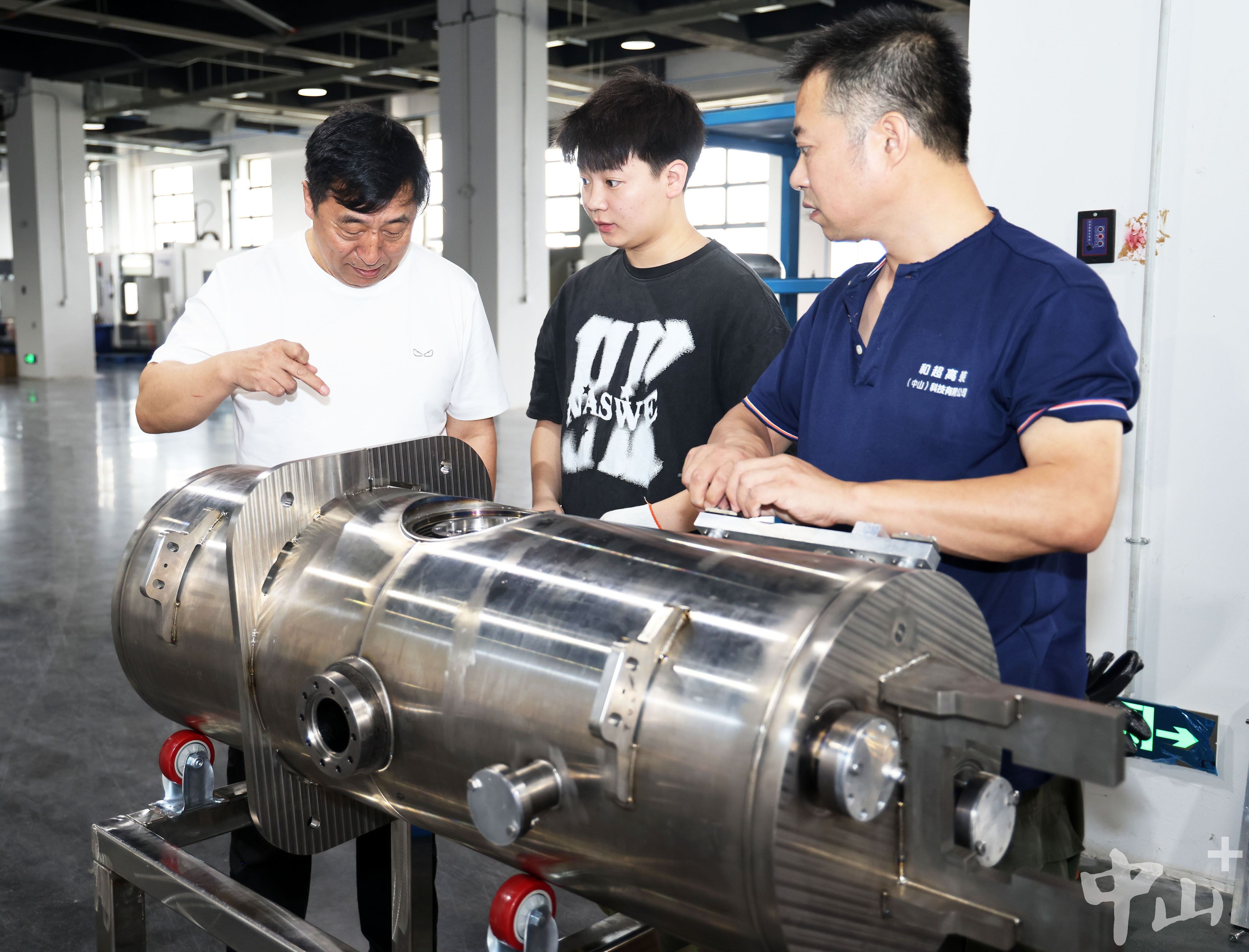
“当时大湾区集中了全国60%的超导加速器项目,超导腔作为核心部件必须就近配套。”他回忆起当年到中山创业的场景,“真正打动我的,是中山的‘创业土壤’——从项目立项到设备通关,政府专班全程跟进,连厂房旁500米的码头都是量身规划,从前设备拆成零件陆运,如今整腔装船出海,效率提升三倍。”
从航天服到超导腔
记者在他公司车间展柜里,见到两件“镇厂之宝”:一件是神七航天服水升华器焊缝切片;另一件是全球首台纯铌9-cell超导腔试验件。它们见证了何景山团队两次改写行业标准的“破冰时刻”。
2006年,神七航天服水升华器焊接遇阻:按国军标检测,焊缝缺陷率达30%,但太空环境模拟测试却表现完美。“传统无损检测卡的是‘纸面标准’,但宇航员生命容不得妥协。”当时,何景山团队解剖500多个样本,发现缺陷集中于非承载区,最终建立“缺陷位置-应力分布”评估体系,让“合格焊缝”定义首次与实际工况接轨。这套标准成为中国航天焊接的“保命法则”。
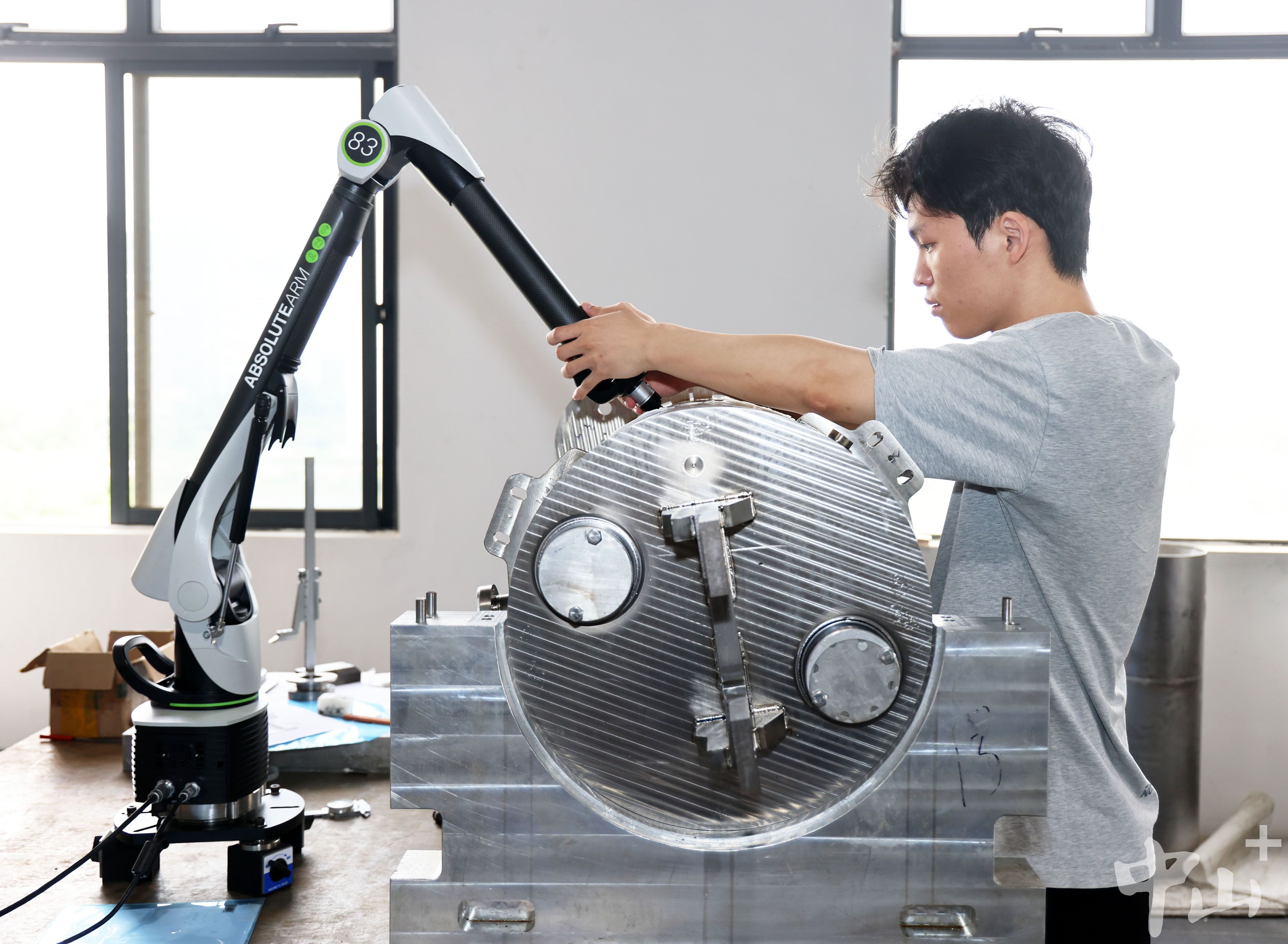
2008年,当何景山转战超导腔时,国外垄断已30年。“他们笑我们‘连铌材都提纯不了’,但我们用哈工大自研电子束焊机,把表面粗糙度做到70纳米——相当于头发丝的千分之一。”他指向显微镜下的腔体质壁,“不是手工打磨,是靠自主数控系统,让机器‘绣’出纳米级精度。”2010年,当中国超导腔性能参数超越国际同行时,德国用户发来邮件:“请告知技术奥秘。”
在中山这么多年,何景山算清三笔“区位账”。第一笔“物流账”:厂房后墙设专用通道,10米高超导腔组件可通过传送带直接装船,破解东北“陆运超限”难题;第二笔“政策账”:作为黑龙江-广东对口合作首项科技项目,中山为其定制“跨境审批绿色通道”,进口设备清关时间缩短60%;第三笔“生态账”:周边300公里聚集全国70%精密加工企业、40%特种金属材料厂,就连腔体内壁超导涂层,都能在佛山找到供应商。
无人区里的“填空者”
2025年春节,何景山在车间贴春联时发现,全球超导腔年产量排行榜更新:中国企业以300套年产能跃居第一,将德国“垄断者”甩在身后。这不仅意味着中国能自主供应“散裂中子源”等大国重器,更将在医疗放疗、工业辐照等民用领域开启千亿级市场。
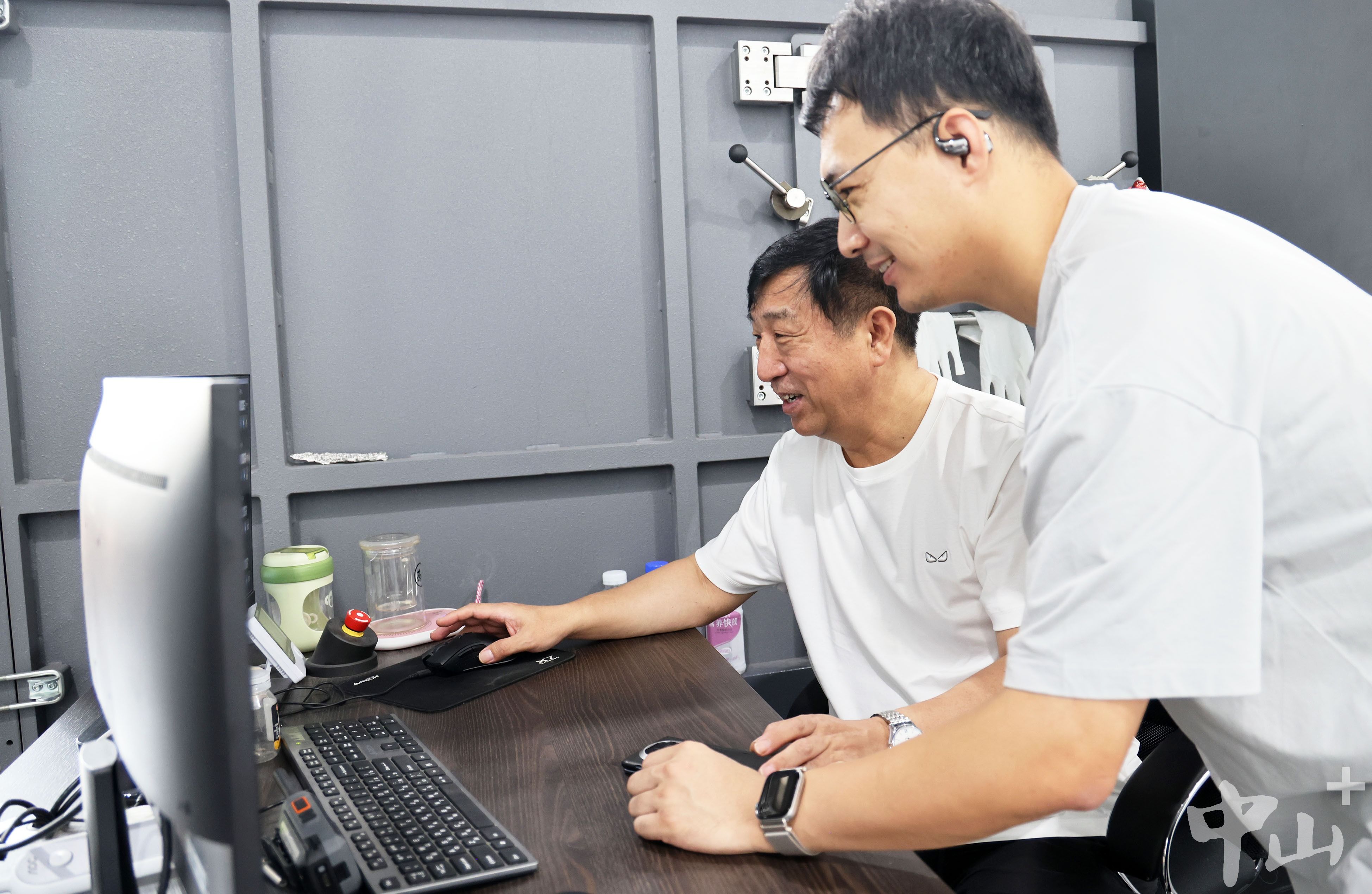
“现在目标是‘从1到100’。”他翻开项目规划书,“超导加速器如同‘粒子手术刀’,可精准杀癌细胞、处理核废料。我们正与生物医药企业合作,未来国产放疗设备核心部件或从这里走向全国。”产业链的辐射效应更深远:本地模具厂为超导腔开发的高精度夹具,已打入半导体封装市场,“大湾区不缺制造能力,缺的是高端装备‘心脏’,而我们正在填补空白。”何景山对记者说。
编辑 陈雪琴 二审 黄廉捷 三审 林志强